Samstag, T-3: Neukauf Beinholz. Teilebau des Korpus und der Schublade und Beinbau mit Fräsung für Kabel. Dazu CNC Fräsung der Vertikalnutblenden. Die Frontplatte für die Schublade mit Einsatz werden erstellt. Fussboden der Schublade wird gesägt & Schiffsplan aufgezogen, erste Laserbeschriftung an Schubladenblende. Alle Korpus- und Schubladenteile sollten und werden fertig. Aktion in der Werkstatt bis Morgens um 4.
Ab ins Auto und Material koofen. Zwei Buchekannten nahm ich mit, denn man weiss ja nun: 4×700 ist mehr als 2500 und sowieso, wer weiss was noch passiert.
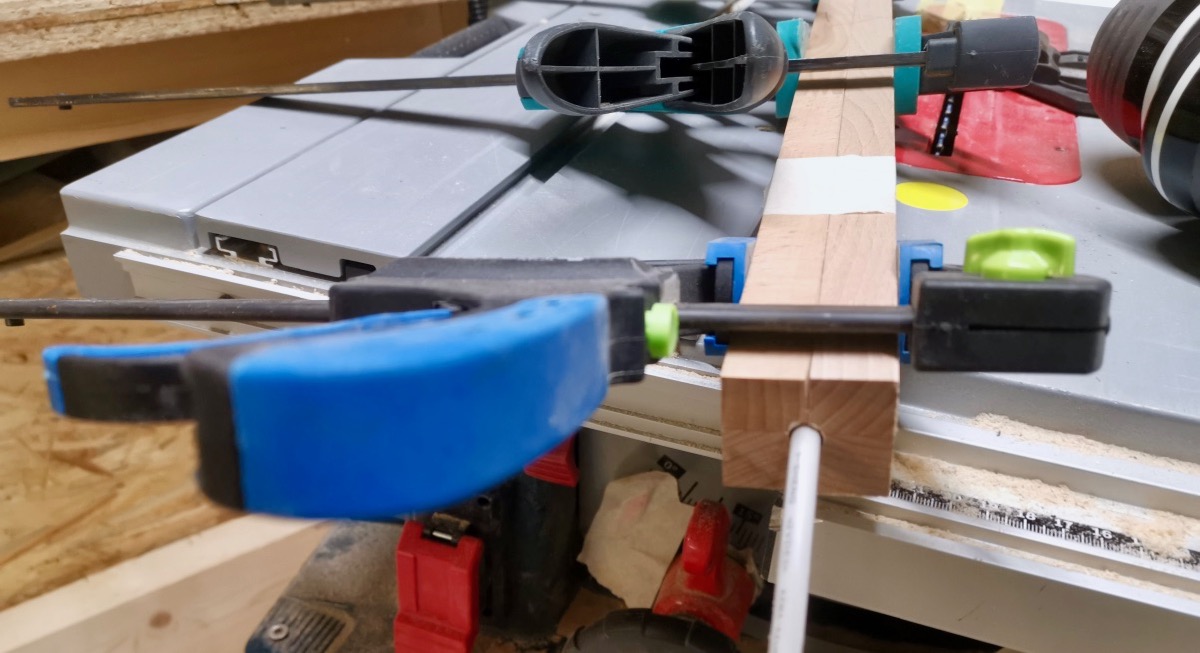
Die neue Idee funktionierte jedoch großartig: Zwei Stücke gesägt, die zusammen die geplante Tischbeinbreite ergeben. Mit dem Halbrundfräser jweils eine Längsnut rein. Beide teile mit Schraubzwingen zusammen und Kabeltest – jau, passt, das Bein konnte geleimt werden.
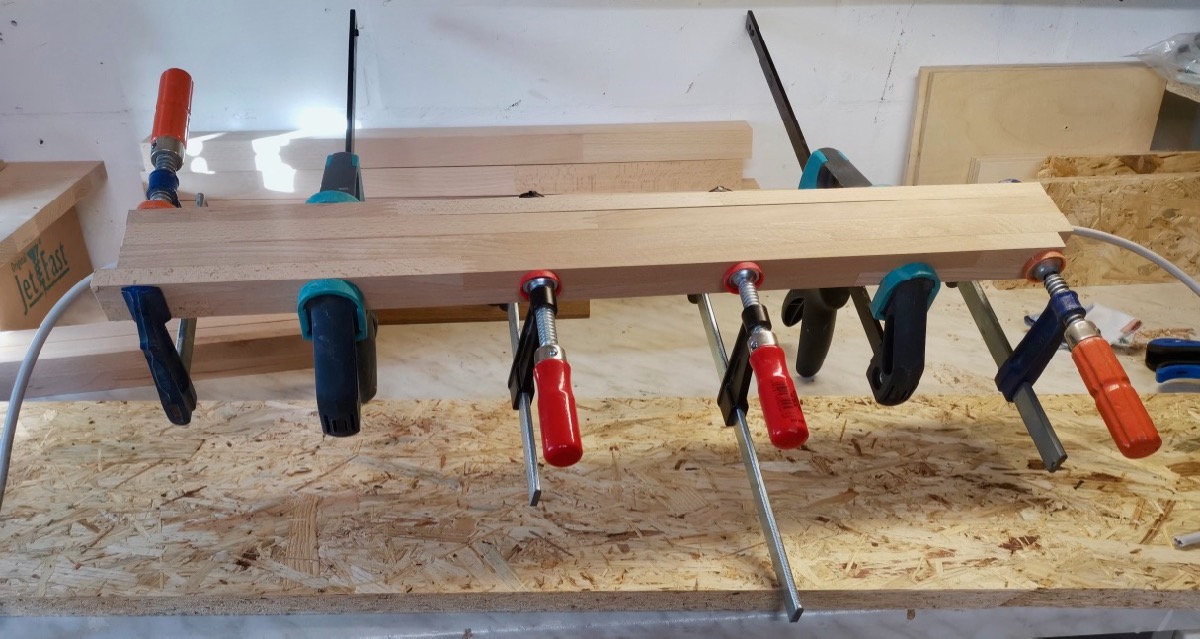
Wärend der Leim aushärtet mache ich mich an die anderen drei Tischbeine. Noch mal eben ein Buchetest auf den Konisch-Mach-Vorrichtung, letzte Feineinstellung bezüglich der Unterlegteilchen um alles so zu haben, wie ich möchte und dann los: Ratzfatz aber mit Ruhe sind die drei Tischbeine und später auch das Vierte konisch gesägt.
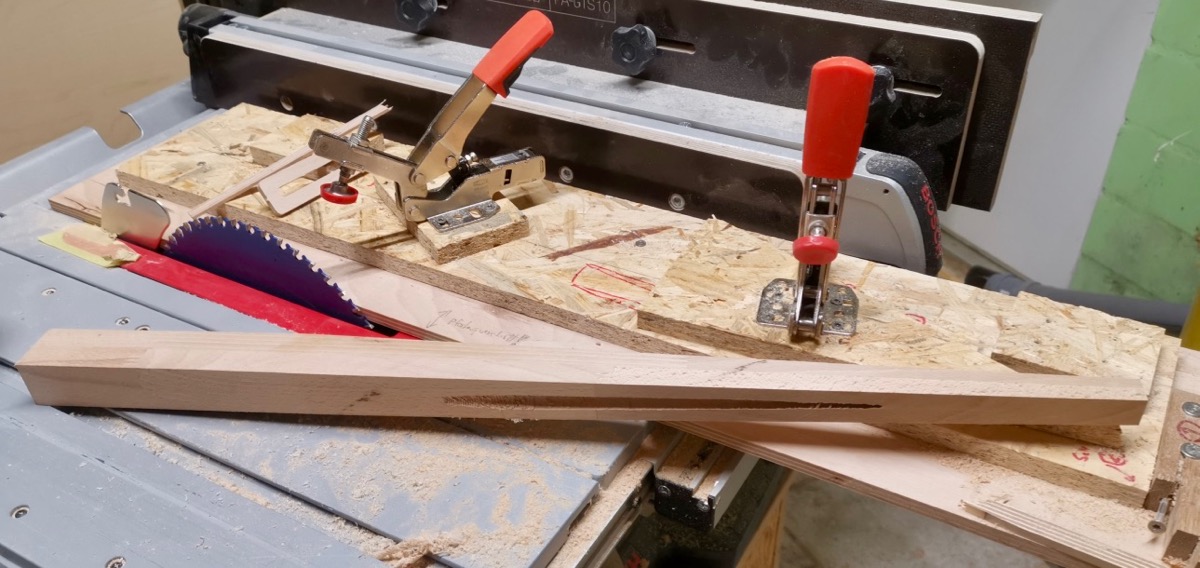
Das Kabelbeinchen benötigt dann noch etwas mehr Zuneigung für den Ein- und Auslass des Kabels. Der Auslass im Schrank fertige ich wieder auf der Fräse und den Auslass unten am Bein mit kleiner Japansäge und Stechbeitel. Langsam traue ich mich mehr mit diesen beiden Werkzeugen zu arbeiten. beide erfordern sehr viel Genauigkeit, sind aber sehr mächtig. Wenn genug Übung vorhanden, kann man wirklich Alles damit machen – ein Maschinenpark ist da nicht wirklich nötig, aber egal, ich „brauche“ meine Maschinen, ich bin noch lange nicht so weit einen großen Teil Handarbeit zu leisten.
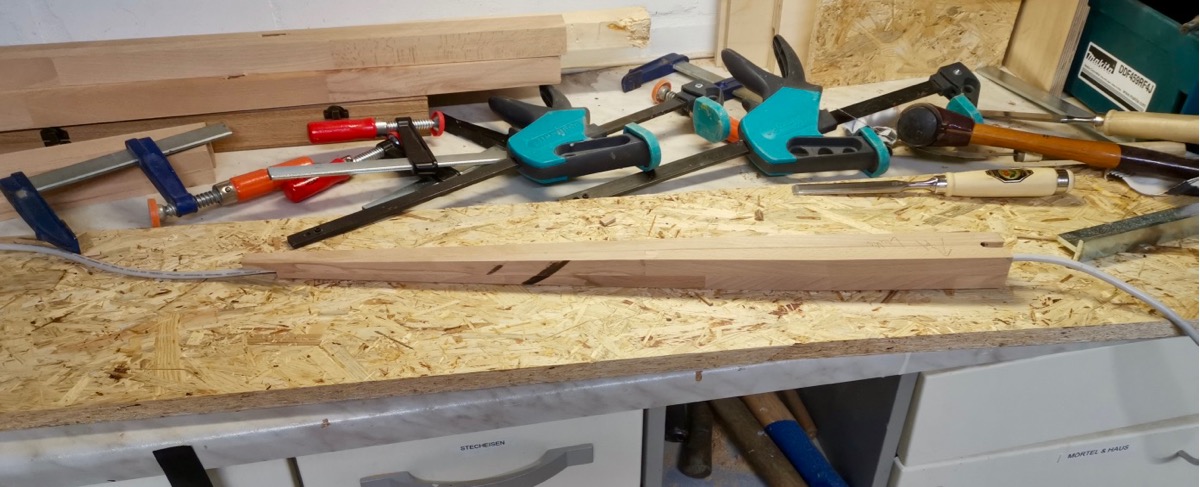
Nach den Beinchen geht es an die Korpusteile, noch ein ruhiger Blick auf meine Zeichnung und dann los: Kurze Holzstücken kann hoffentlich auch der Fuscher ohne große Tests sägen. Kann er auch, doch ist das nächste Zwischenprojekt schon klar: Der selbstgebaut Schiebeschlitten für Tischkreissäge hat etwas Spiel, hat mich nie wirklich gestört – jetzt tut es das aber. Das muss „Vernünftig“, doch nicht jetzt, die 5/10tel schleife ich später.
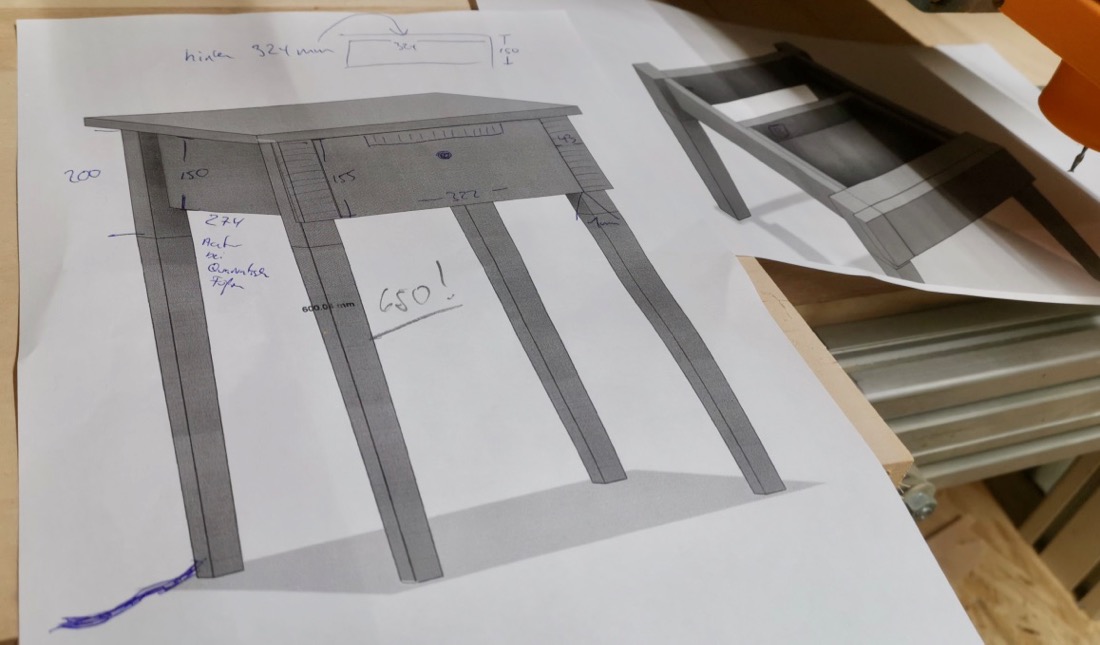
Nachdem die Korpusteile gesägt sind versuchte ich mich zum x. Male an Holzdübeln. irgendwie war das bisher nicht mein Ding und auch nie wirklich mit Erfolg gekrönt. Die Bauteile kamen irgendwie nie da zusammen, wo ich sie gerne zusammen haben wollte ;-) Im Vorfeld überlegte ich mir ja sehr angestrengt ob ich wieder versuche das mit einer Maschine zu erschlagen, doch ich entschied mich mehrfach dagegen (und wieder dafür, und wieder dagegen ;-). „Lieber Fuscher, Du baust jetzt mal so ein Fuschstückchen und dafür hast Du nun genug Maschinen, jetzt muss mal Übung und Ruhe ran. Und wenn Du das hinbekommst, dann darfste Dir auch nen Maschinchen koofen. Ist wie inner Schule, erstmal von Hand Rechnen, danach der Taschenrechner.“ Und tatsächlich, ich hörte auf mich und fand mich bei Holzdübeltests wieder. Für mich stellten sich so kleine „Einlegpieksernüsel“ als pragmatischster Ansatz heraus. Die hatte ich mir irgendwann mal vorsorglich zugelegt. Kleine Teilchen, die man in die Löcher des ersten Teils legt. Dann wird das nächste Teil in exakter Position leicht draufgedrückt/gehämmert und schon hat man Abdrücke für die neuen Löcher der Holzdübel.
Man merkt an solch einfachen Dingen, der Fuscher hat zwei Linke Hände. Und zwar riesengroße. Jeder dieser Schritte erfordert dem Fuscher ne ganze Menge ab, auch wenns nur kleine Holzdübel sind.
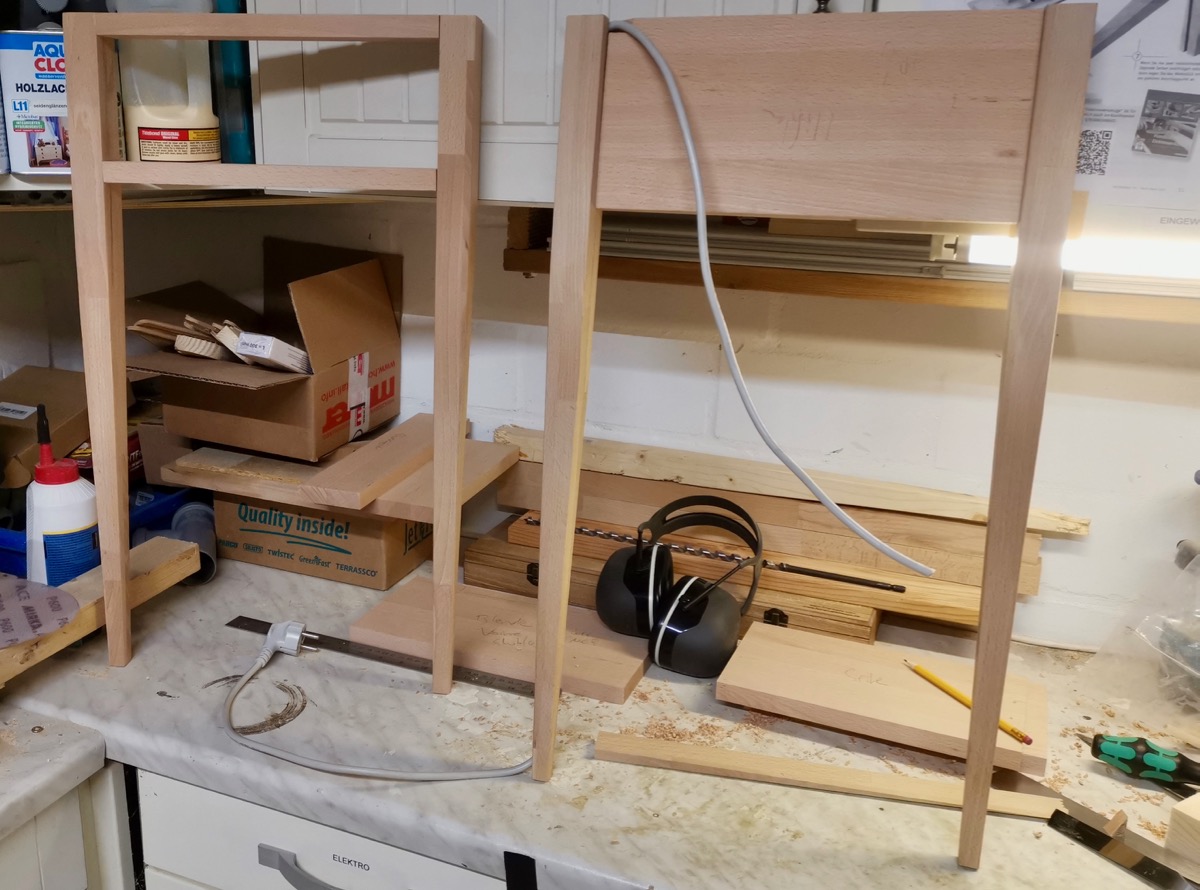
Das ganze funktioniert in diesem Falle wirklich fein und mit jeder Bohrung verliere ich die Angst, jedoch nicht ohne die Ruhe zu verlieren: Unterschiedliche Materialstärken erfordern unterschiedlich tiefe Löcher und Durchbohren will ich auf keinen Fall. Alles passiert jetzt ja mit dem „guten“ Buchenholz. Durchgehende Lamellen hat es und ist hier nicht so zu bekommen. Wäre der Verschnitt größer als mein gekoofter Vorrat wäre es mit dem Zeitplan vorbei. Es klappt jedoch wirklich gut. Irgendwann zwischendurch muss ich nur ein Korpusteil neu herstellen, da ich mich verfusche. Knappe 400mm in 150mm breit. Das kann mein Vorrat verkraften ;)
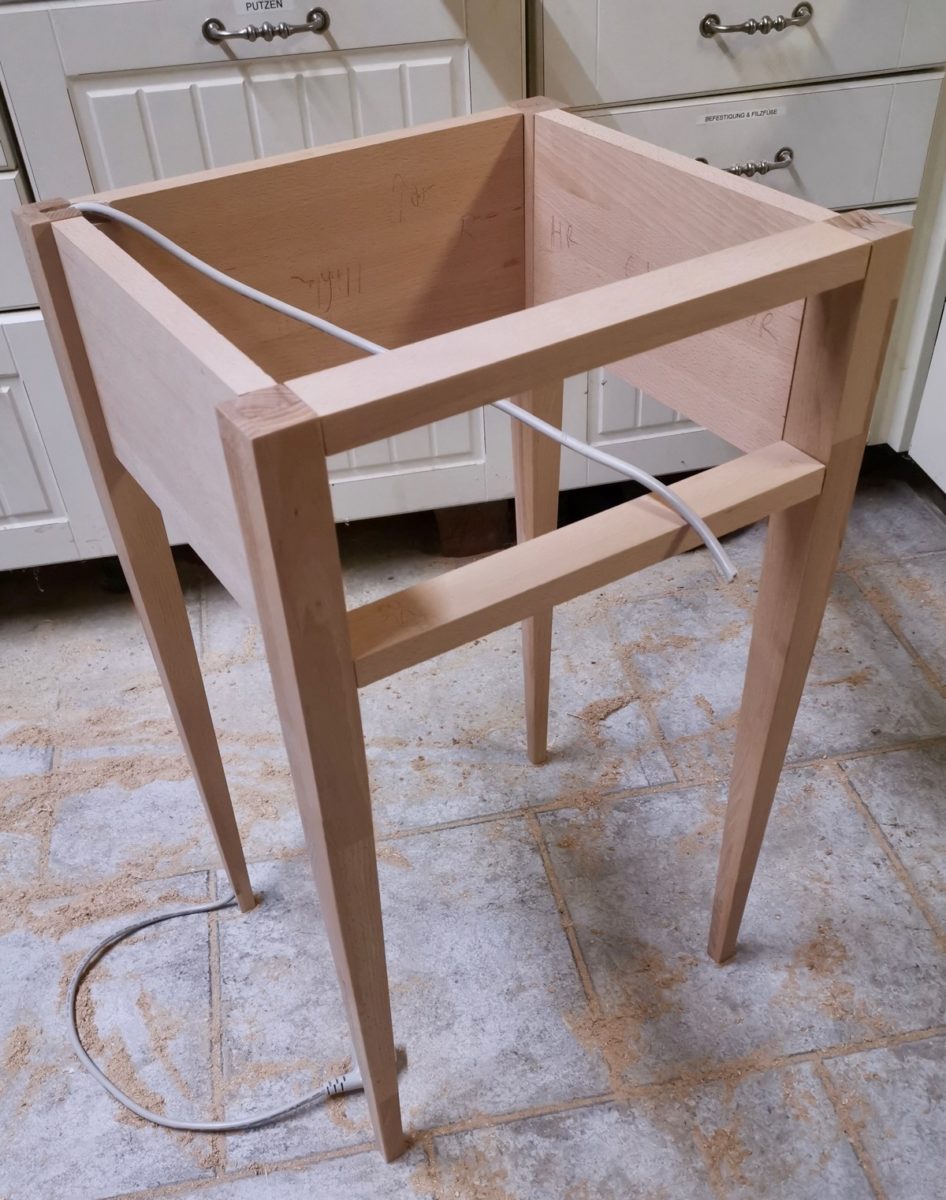
Der Vorrat ist übrigens das Eine. Das Andere ist das die Maserung auch zueinander passen soll. Verfuschen kann also doppelt ärgerlich sein. Ist es beim Korpus beim Beistelltischchen und den einzelnen vier Seiten noch egal, so ist es bei der Front, wo mehrere Teile eine Sichtseite ergeben nachher unschön wenn die Maserung nicht zusammenpasst.
Nach dem Korpus nute ich das Holzteil für den Schubladenkorpus. Erst auf Länge nuten, dann auf einzelne Holzeile auf Länge sägen. Ich entscheide mich bei der Schublade gegen Gehrungsschnitt, weil ich mir einrede das es „einfacher“ ist. Werde ich nicht noch mal machen: Mit Gehrungsschnitt und meinen Korpusbandzwingen ist es einfach sehr einfach und man erlangt eine sehr gute Rechtwinkligkeit. Beim verleimen auf Stoss ergab sich am Ende dann doch wieder eine Ungenauigkeit (warum auch immer ;-) Die hätte ich mit Gehrungsschnitt vermeiden können – zumindet bin ich da der Meinung, und drum mach ich das nächstes Mal auch wieder so, fertig aus. Dieses Mal wird wieder geschliffen. Natürlcih nicht nur die Fuscherei, sondern alle Korpus und Schubladenteile, jeweils zweimal mit 240er und 600er. Danach alle Teile Anfeuchten, trocknen lassen und noch mal mit 600er Schleifen.
Die Rückwand der Schublade erhät noch einen Ausschnitt für die USB Steckdose – kar, das ein normaler 50mm Ausschnitt nicht reicht. Das Ding ist so unförmig, das ich mich langsam mit verschiedenen Werkzeugen rantaste – am Ende passt es dann wirklich gut und mit Blende sieht es auch gut aus ;)
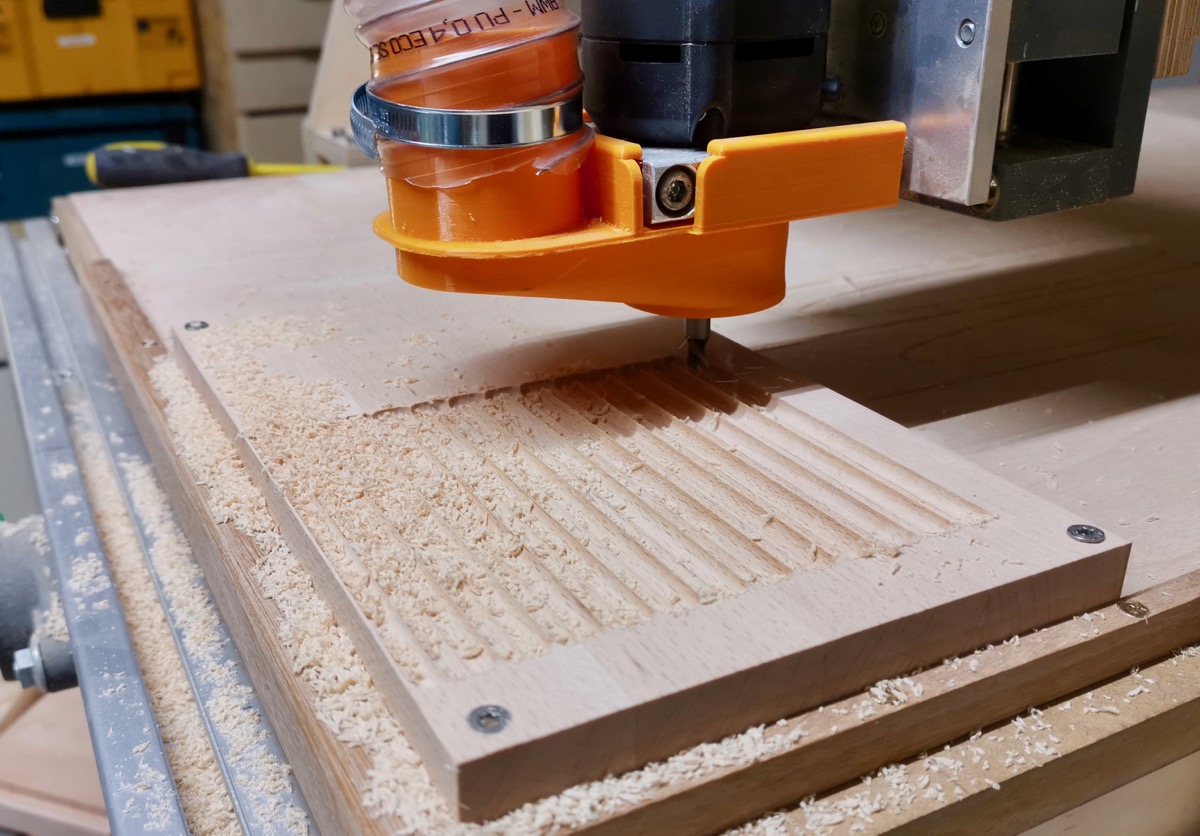
Dann ist die CNC Fräse dran. Die markanten Designelemente des bestehenden Schrankes müssen nachgestellt werden. Die jeweiligen Frästdatein hatte ich ja vorbereitet und musste sie nur wenig anpassen. Ich fräste als erstes die Horizontalnutblenden in einem Stück. Ich hatte das ja schon mal ausprobiert und nachdem ich ja die CNC Fräse mit einem schönen Anlegeeck in der Vorbereitungszeit versehen hatte, klappt das auch mit dem drehen und hochkannt fräsen der Teile sehr gut. Die fertigen Teile wurden danach dann auf der Tischkreissäge „gleichgesägt“, beim Fräsen entstanden etwas unterschiedlich hohe Nuten. Ich denke das ist der Holzungenauigkeit geschuldet. Das Holzmaterial ist auf wenige 10tel unterschiedlich dick. nach dem sägen sahen beide gefrästen Seiten sehr harmonisch aus. Beide Teile habe ich etwas breiter gefertig als später benötigt, damit ich das später feinjustieren kann. Die Nuten wurden übrigens mit einem 6mm Fräser in 5.5mm Abstand, 4mm tief gefräst.
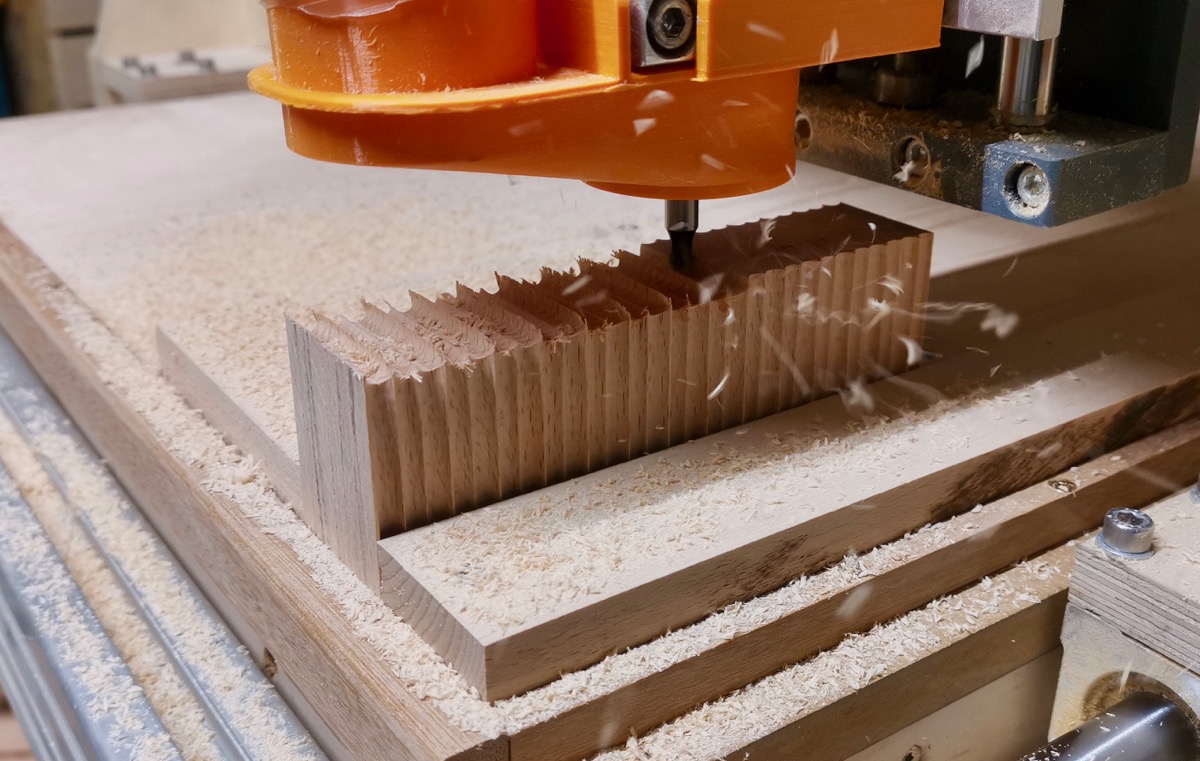
Nachdem Horizontal fertiggstellt war ging es an Vertikal. Das hatte ich noch nicht probiert da ich auch hier etwas auf den 20mm Falbrundfräser warten musste. Schon bei den horizontalen Nuten musste ich etwas tüddeln bis ich den perfekten Fräsabstand & Tiefe raus hatte. So auch hier: Die erste Fräsung ging gut, gefiel mir aber von der Tiefe nicht so. Also Teil umgedreht und den rest des Stückchens noch genutzt. Da ich ja nur einen schmalen Streifen benötigte war das noch vollkommen ausreichen. Beim zweiten mal gefiel es mir. Jede Änderung an der Fräsdatei bedeutet übrigens einen Gang an den Schreibtisch, und dieser steht unweit des Bettes in dem die Froo schon lange Schlief.
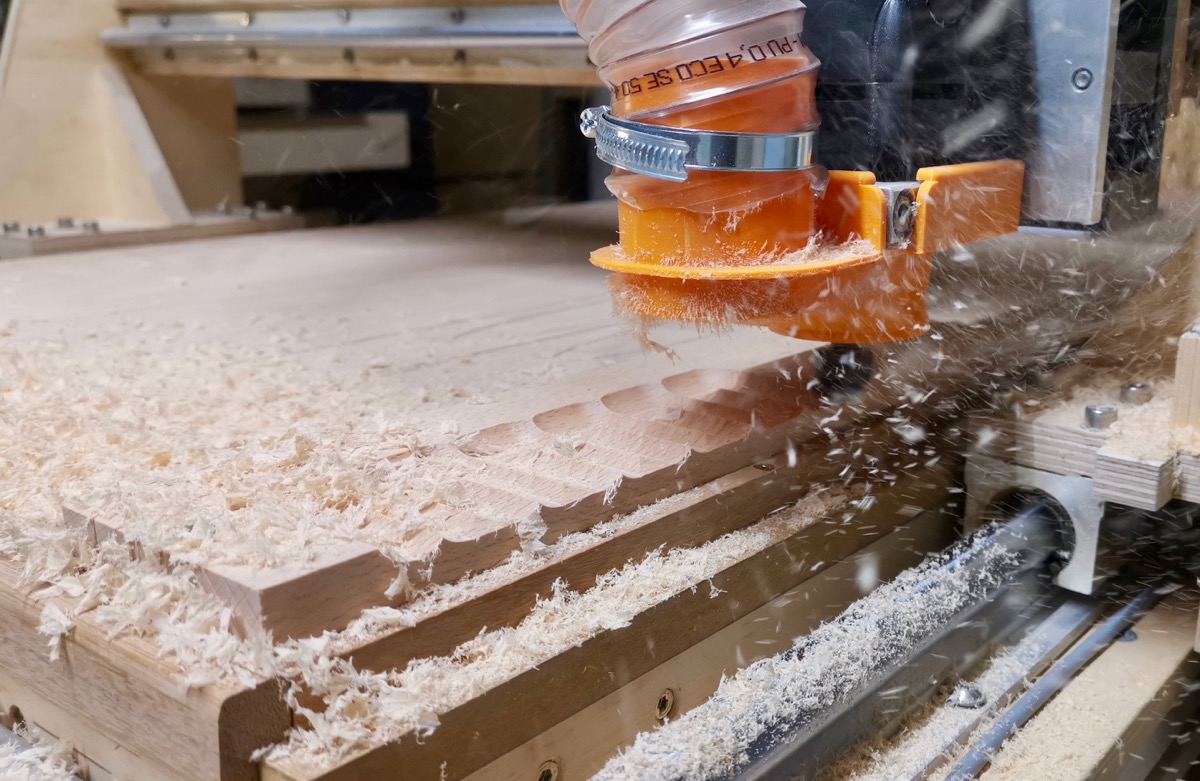
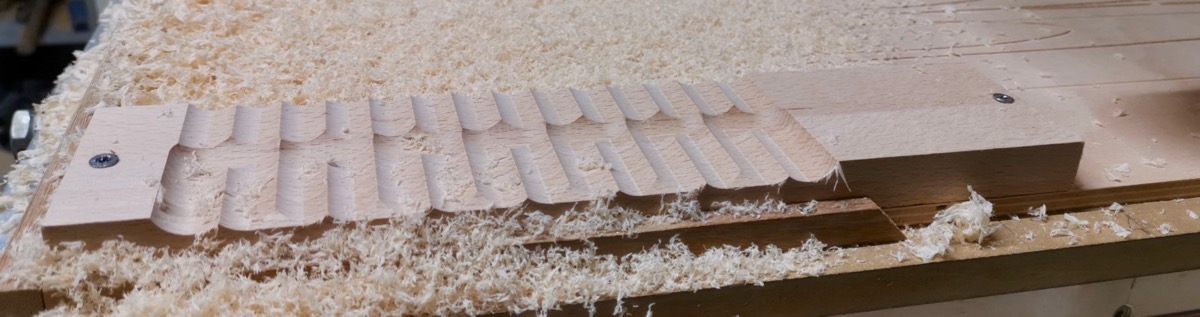
Nachdem auch das Teil geschafft war benötigte die Frontblende der Schublade auch noch einen passenden Ausschnitt in den die Leiste passt. Fast hätte ich einfach ein fixes Mass genommen und losgefräst. Glücklicherweise warnoch so viel Konzentration vorhanden das ich noch an die Vertikalnuten dachte – wenn möglich sollten ja alle Nuten vollständig sein, würde ja doof aussehen, wenn die letzte Nut auf einmal bei der Hälfte abgeschnitten wäre. Also, kein fixes mass aus dem Kopf. Das Mass musste der tatsächlichen breite meines gefrästen Stückes betragen. Also wieder hoch zum Schreibtisch und Fräsdatei angepasst.
Es klappte wieder erstaunlich gut: Schön an meiner Anlegeecke zwischen aufgeschraubten Holzteilen auf dem Frästisch aufgespannt und los. Ich wählte einen 3,175mm dicken Fräser. Dünner ging leider nicht, da ich knappe 20mm ins Holz musste und nur diesen Durchmesser habe ich in ausreichender Länge. Mir war klar, das an den Innenkannten des Ausschnittes dann Rundungen entstehen welche ich dann entfernen muss. Die praxis zeigte aber später das bei nur einem leichten Schleifen der Vertikalnutblendleiste die Ecken genügend abgerundet waren um dort perfekt reinzupassen.
Ich wählte den Ausschnit um einen „Müh“ weniger breit als meine Blendleiste umd die Leiste nachher von Hand in die perfekte Breite zu schleifen. Dieses Vorgehn funktionierte sehr gut. Ein „Müh“ ist übrigens wenige 10tel Milimeter. Das Ding sass perfekt und konnte verleimt werden. Nachdem der Leim ausgehärtet war sägte ich an der Tischkreissäge die Blendleiste mit der Schubladenblende bündig. So hatte ich mir das vorgestellt. Grandios.
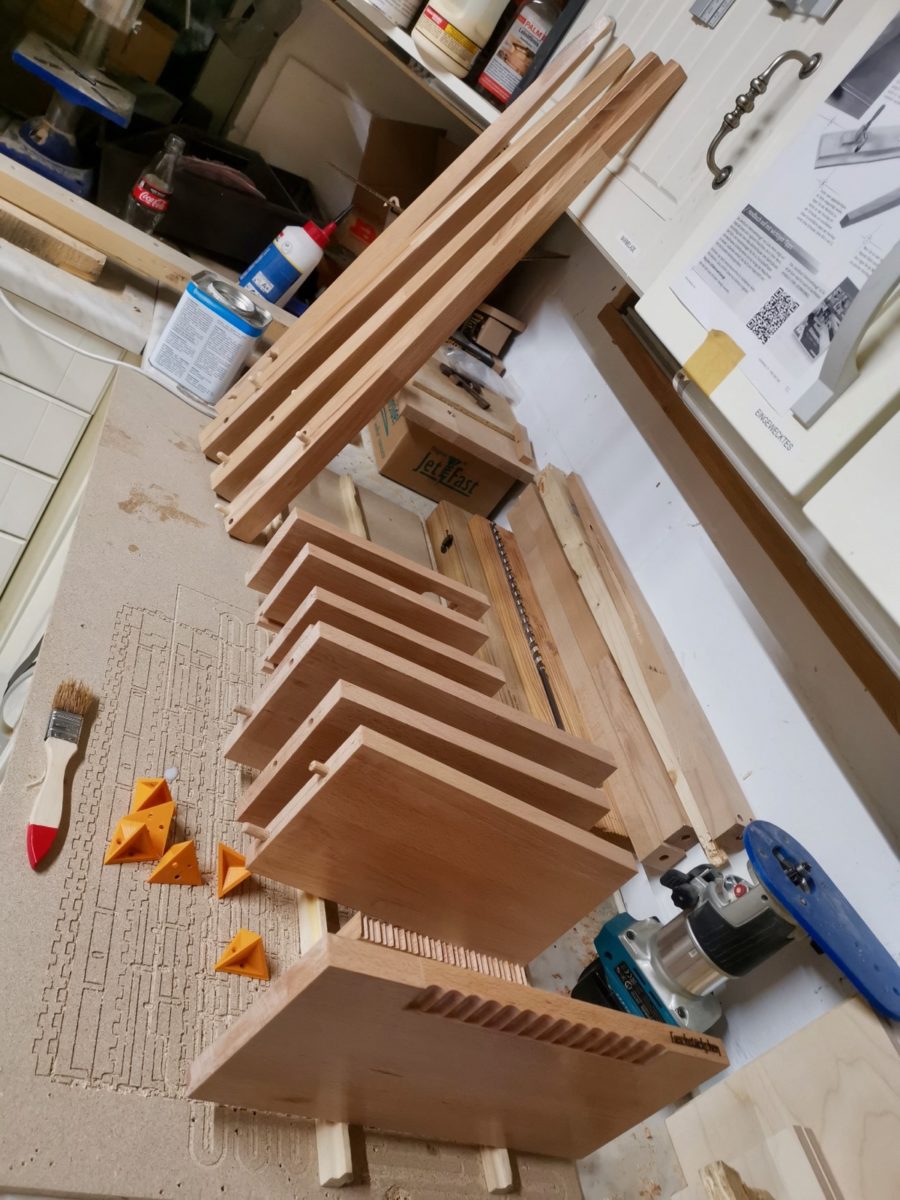
Damit waren Sägearbeiten für heute beendet. Alle gefertigten Teile wurden noch Lackiert und die Schubladenblende wurde oben rechts auf der Kannte mit einem Fuschstückchen Logo belasert. Ich bin immer wieder von diesem kleinen Chinagadget begistert an welchen „unmöglichen“ Stellen man da was hingelaster bekommt.
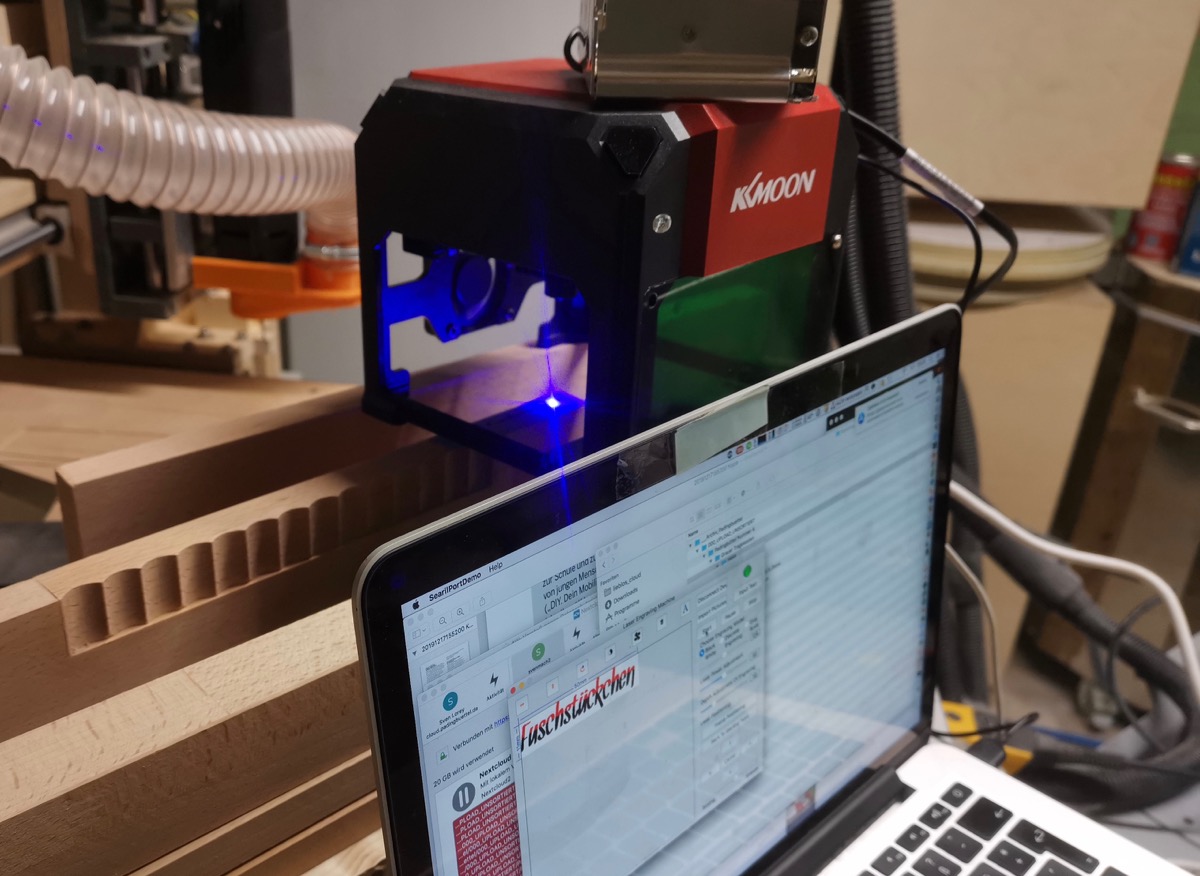
Lasern ist übrigens nichts für feine Lungen. Ich habe ein Feinstaubmessgerät um die Belastung der Luft beim Sägen zu messen. Seitdem ich konsequent auf Absaugung achte bleibt das alles im gut ertragbaren Rahmen. Und egal wie ungenau dieses Teil sein mag, beim Lasern flippt das Teil jedes Mal wiederholgenau aus. Man kann das ja quasi schmecken!, dass da was beim Lasern in der Luft liegt. Die Anzeige bestätigt das dann auch. Wo sonst eine ein bis mittlere zweistellige Zahl steht, werden jetzt kleine bis mittlere dreistellige Zahlen angezeigt. Das kann auf Dauer nicht gut sein und so erwische ich mich dabei die Wartezeit auch mal in der dunklen Nacht draußen zu verbringen.
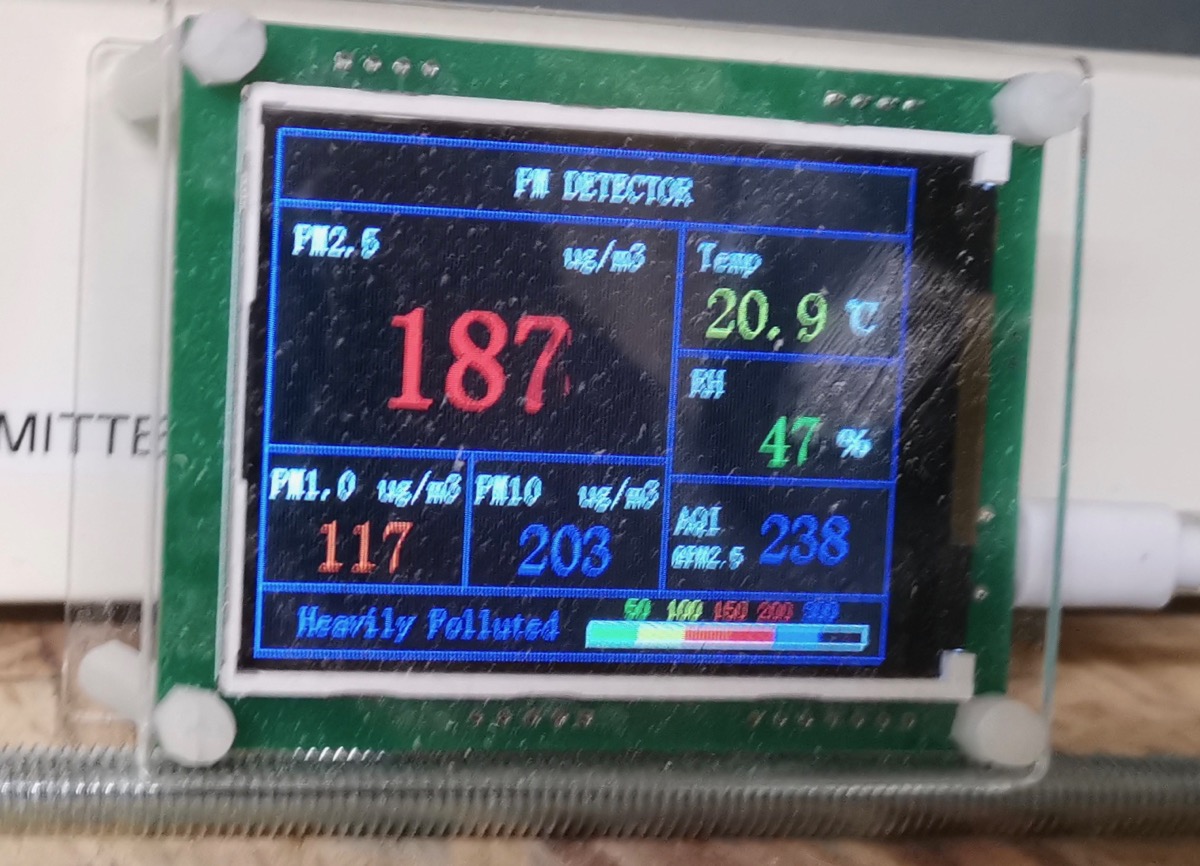
Nach getaner Arbeit belohne ich mich früh Morgens noch mit etwas Lustigem Taschenbuch Lesen. Wer mich kennt weiss, dass ich ein LTB nur mit etwas zu Essen lesen kann, oder auch umgekehrt ;) Dabei fällt mein Blick auf den ausgeschnittenen Schiffsplan. Zack, wieder in die Werkstatt: Schiffsplan auf den Schubladenboden aufziehen.
Um vier wandere ich dann wieder nach oben. Dieses Mal nicht zum Schreibtisch, sondern ins Bett.
Morgen geht es weiter…